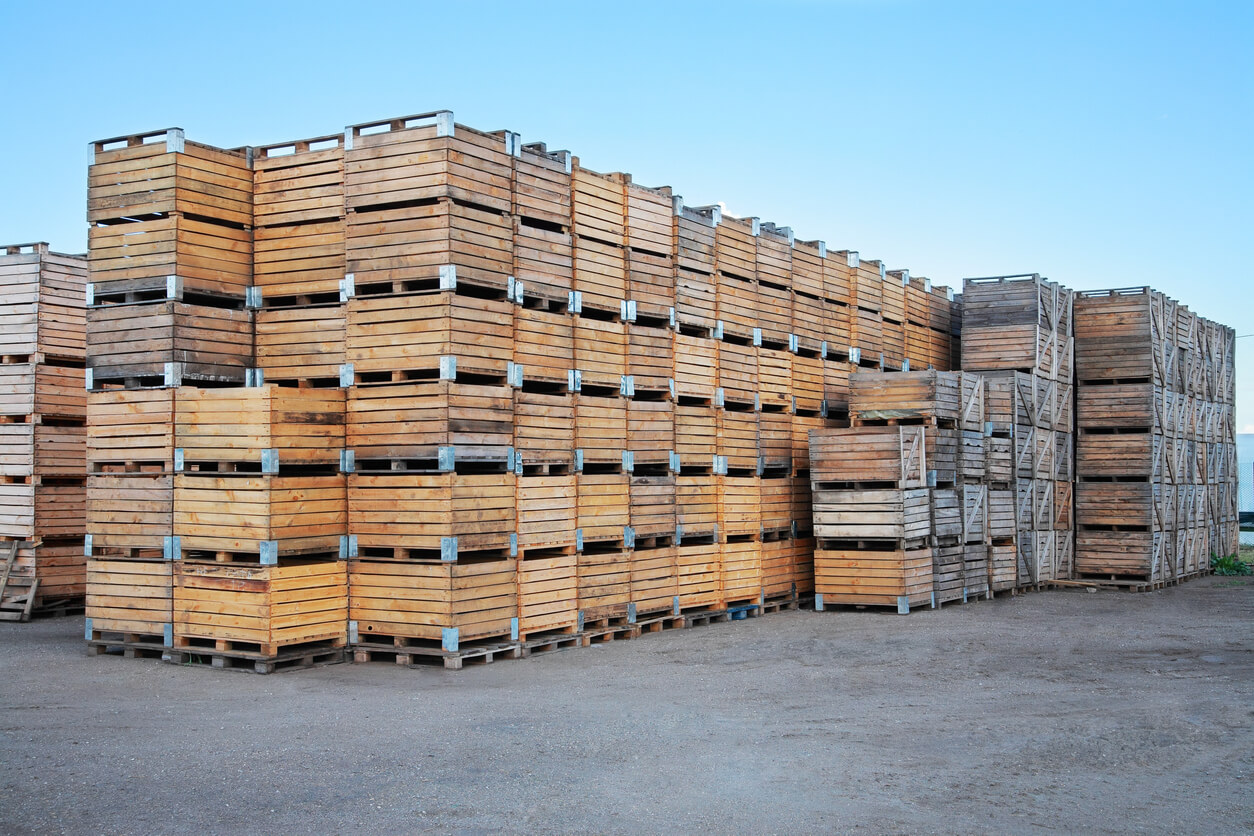
All about palletizing: types of pallets, loads, and logistics optimization
Pallet racking is essential in logistics and storage. Pallets play a fundamental role in transportation, improving the efficiency of goods
Palletizing merchandise is a key process in modern logistics.
It involves stacking products on pallets, facilitating their handling and transportation. This method improves efficiency and safety in the supply chain.
Furthermore, palletizing reduces loading and unloading times, optimizes available space, and lowers logistics costs. It also increases productivity by minimizing product handling and protects both merchandise and operating personnel.
Palletizing is an essential process in logistics and product transportation. It involves stacking goods on pallets to facilitate handling and transportation.
Palletizing involves placing goods on a platform, usually a pallet, which facilitates their storage, handling, and transportation.
These pallets can be easily handled using equipment such as forklifts and pallet trucks.
The main objective of palletizing is to optimize space and improve supply chain efficiency by grouping products into standardized unit loads.
Pallet racking has its origins in the first half of the 20th century. With the advent of the forklift in the 1920s, the need to standardize loading platforms to improve efficiency in goods handling became apparent.
During World War II, the use of pallets increased to speed up the loading and unloading of supplies, and since then, they have become a standard in the logistics industry. Over the decades, pallet design and materials have evolved, adapting to different needs and emerging technologies.
There are several types of palletizing, each suitable for different contexts and logistical needs.
Palletizing goods in logistics offers multiple benefits. Below are the most notable advantages in various crucial aspects of the logistics process.
Pallet racking allows products to be grouped on pallets, maximizing available space in warehouses and on transportation vehicles. The orderly arrangement of loads facilitates access and handling of goods, increasing efficiency.
The use of pallets makes it easier to adapt merchandise to different shelving and storage systems. This contributes to more efficient space management, both in conventional and automated warehouses, maximizing storage capacity.
The implementation of pallet racking significantly reduces vehicle loading and unloading times. Handling goods individually on pallets speeds up these processes and reduces vehicle downtime in warehouses.
The use of forklifts and pallet trucks to handle palletized goods allows for quick and safe movements. This streamlines logistics processes and minimizes the physical effort required by staff.
Palletizing reduces the need for direct handling of goods by personnel, which reduces the risk of damage and errors. This increases the efficiency and productivity of logistics operations.
Grouping products on pallets facilitates faster storage operations by ensuring load stability. This helps maintain order and security in the warehouse, as well as streamlining inventory turnover.
Pallet racking reduces the risk of workplace accidents by minimizing individual handling of heavy or bulky products. The use of equipment such as forklifts improves staff ergonomics, reducing unnecessary physical strain.
The orderly and stable arrangement of goods on pallets provides greater protection during transport and storage. This reduces the risk of damage, ensuring that products arrive in optimal condition at their final destination.
The efficiency achieved through palletizing reduces the costs associated with loading and unloading operations. The process is streamlined, reducing the time and resources required for these activities.
Optimizing space in transport vehicles through palletizing improves fleet efficiency. This allows for transporting a greater amount of merchandise on each trip, reducing fuel costs and improving the duration of logistics routes.
Pallet racking systems allow for more efficient use of space and improve various aspects of merchandise storage and transportation.
System | Description |
---|---|
Conventional palletizing | This is one of the most common methods and is based on the use of standard pallets. It is suitable for a wide variety of products and allows for easy handling with forklifts and pallet trucks. It optimizes the use of warehouse space and facilitates loading and unloading. |
Compact pallet racking | Maximizes space utilization by reducing aisles between shelves. It's ideal for large volumes of stock and maximizing available storage space. |
Mezzanines and self-supporting floors | These are structures within compact pallet racking that do not require additional support from the building. Mezzanines allow height to be utilized by adding additional levels, and self-supporting structures support both the loads of the products and the warehouse structure. |
Automated warehouses | They use advanced technology to optimize the storage and handling of goods. Automated systems achieve greater precision and speed in logistics processes. |
Warehouse automation | It involves the use of robots, conveyor belts, and automated management systems to handle products. It reduces human intervention, minimizes errors, and improves operational efficiency. |
Storage and distribution systems | They enable efficient inventory management and a rapid response to market demands. They use advanced software to control the flow of goods, perform real-time inventories, and optimize distribution routes within the warehouse. |
The fundamental components of pallet racking allow for efficient and safe handling of goods. These elements are essential for optimizing product logistics and storage.
Pallets and skids are the base on which merchandise is stacked, providing a stable platform for storage and transportation.
Pallet materials vary depending on the handling requirements of the goods and the conditions they face.
Pallet wrapping is essential for securing goods on pallets using plastic film. This equipment improves load stability and protects them from external conditions, such as moisture and dust.
There are several types of pallet wrappers, ranging from manual to fully automatic, allowing for greater efficiency in the packaging process.
Packaging systems are crucial for protecting products during transportation and storage. They ensure that merchandise arrives at its destination in perfect condition.
Cardboard boxes are a popular option due to their versatility and cost. They are lightweight, recyclable, and easy to handle, providing adequate protection for a wide variety of products.
These systems, together with pallets and wrappers, form the essential structure for an efficient and safe palletizing process.
Pallet racking continues to evolve with the incorporation of new technologies and trends in logistics and storage.
Automation and robotics are revolutionizing the way palletizing is done. Palletizing robots are used to stack and organize goods accurately and quickly. These automated systems reduce human error and increase process speed.
Forklifts and automated transport systems also play a crucial role. They enable the efficient movement of pallets within warehouses and distribution centers, significantly improving overall productivity.
The use of sensors and real-time monitoring technology is transforming supply chain management. Sensors installed on pallets provide real-time data on the location and condition of goods. This information is crucial to ensuring product integrity during storage and transportation.
Real-time monitoring also makes it easier to identify potential problems, such as improper storage conditions or unauthorized movements. This enables a rapid and effective response to ensure the safety and quality of the goods.
New trends in logistics are driving significant changes in palletization. The growing demand for e-commerce services has led to the need for more flexible and dynamic storage systems.
The use of automated storage systems and the integration of advanced technologies such as artificial intelligence and machine learning are transforming logistics. These systems enable space optimization and improved operational efficiency.
Furthermore, the focus on sustainability is driving the development of pallets made from recycled and eco-friendly materials, thus contributing to a greener and more sustainable supply chain.
Pallet racking is essential in logistics and storage. Pallets play a fundamental role in transportation, improving the efficiency of goods
This container has all the advantages: large capacity and great maneuverability.