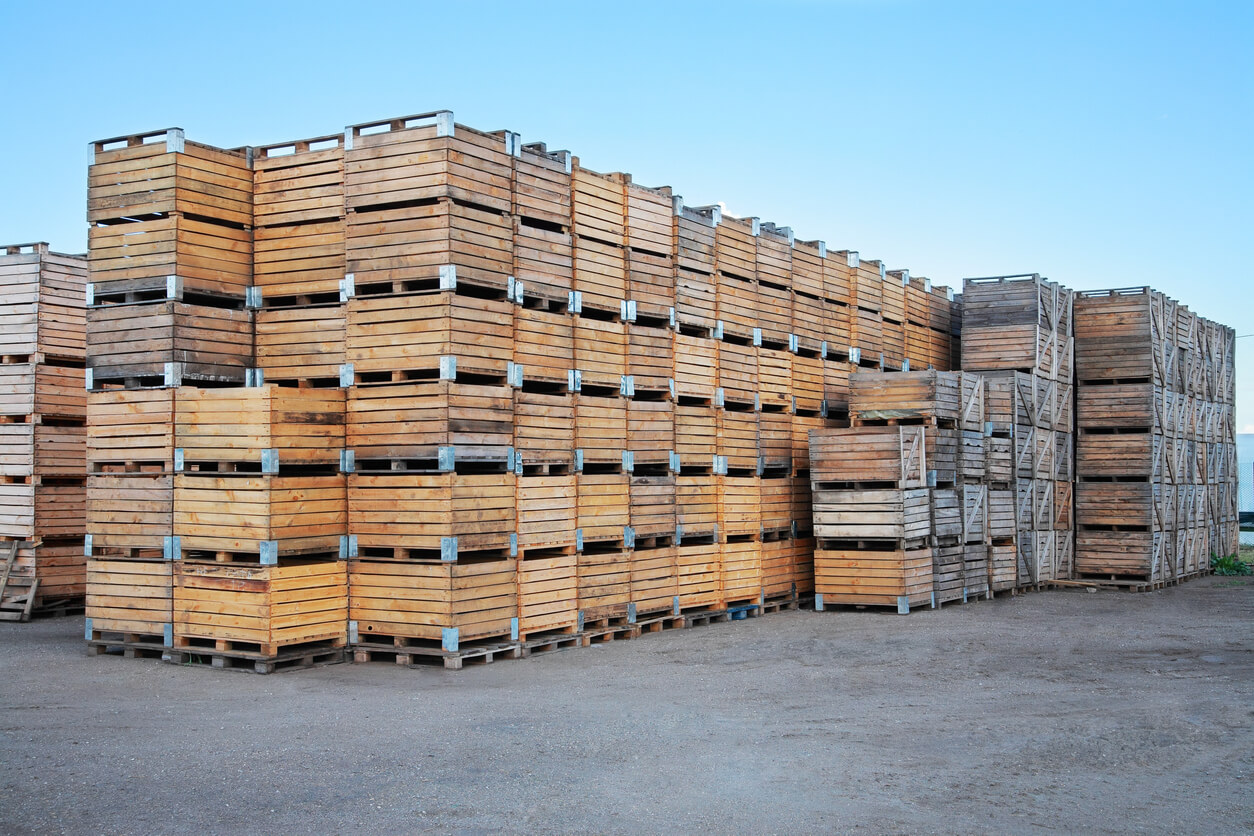
All about palletizing: types of pallets, loads, and logistics optimization
Pallet racking is essential in logistics and storage. Pallets play a fundamental role in transportation, improving the efficiency of goods
Cross-docking is a logistics system in which goods are distributed directly to the end user without going through storage. This process allows for cost savings, improved product quality, and reduced delivery times. In cross-docking, goods are received and loaded onto the transport medium immediately. There are different types, such as pre-distributed, consolidated, and hybrid, adapting to the specific needs of each company.
It is a logistics strategy that seeks to optimize the supply chain by distributing goods without the need for intermediate storage.
Cross-docking is a logistics process in which products are received at a distribution center and shipped to customers almost immediately, bypassing storage.
This methodology aims to minimize handling and storage times, achieving greater efficiency in the supply chain.
The term “crossdocking” comes from English and can be literally translated as “crossing docks.” It refers to the practice of transferring products directly from an incoming vehicle to an outgoing one, optimizing the flow of goods.
This practice began to gain popularity in the distribution and retail industries during the second half of the 20th century, especially in the United States. Its implementation has spread over the years to encompass different economic sectors.
Cross docking differs significantly from traditional storage in several ways:
Aspect | Traditional storage | Cross docking |
---|---|---|
Storage time | Products remain in the warehouse for long periods. | The holding time is minimal, they are quickly transferred to shipping. |
Operating costs | Higher costs for inventory management, handling and storage. | Significant cost reduction by eliminating intermediate storage. |
Workflow | Receiving → storage → picking → shipping. | Reception → sorting → direct shipping. |
Efficiency | Slower processes, greater operational load. | Greater agility and efficiency in distribution. |
Space required | It requires large surfaces to store products for longer periods of time. | Less storage space required. |
Inventory level | High levels of accumulated stock. | Low or even no inventory. |
Rotation speed | Slower inventory turnover. | High turnover of goods. |
Risk of obsolescence | Greater risk when holding stock for a long time. | Reduction of the risk of obsolescence or deterioration. |
Traceability and control | More controlled, but less agile process. | It requires good synchronization and real-time traceability. |
Technological requirements | Less technological dependence. | It requires advanced information systems and efficient logistics coordination. |
These differences make cross-docking an attractive option for companies looking to optimize their logistics operations and reduce costs.
Cross-docking offers multiple advantages to the logistics and distribution of goods, facilitating a more efficient and profitable supply chain.
Implementing it allows companies to significantly reduce operating costs by eliminating the need to store products in inventory. This system minimizes costs associated with storage space, the labor required to manage inventory, and the risk of merchandise spoilage.
It significantly accelerates the merchandise distribution process, reducing the time it takes for products to reach the end customer. By avoiding intermediate storage stages, faster and more efficient delivery is achieved.
By reducing the time products spend in storage, their quality is better preserved, especially in the case of perishable or fresh goods. By minimizing handling and transfer points, the risk of damage and spoilage is also reduced.
There are different methods, each adapted to the logistical and operational needs of companies.
Pre-distribution is characterized by pre-sorted and labeled merchandise for direct delivery to destination points. This way, upon arrival at the distribution center, the products are immediately sent to the appropriate transportation system without the need for additional handling.
The main features of the pre-distributed include:
Consolidation involves receiving goods from different suppliers and then combining them to form consolidated shipments to recipients. This method is used to optimize transportation space and reduce logistics costs.
The consolidation process follows the following steps:
Hybrid cross-docking combines elements of pre-distributed and consolidated cross-docking. This approach is used when some goods can be pre-distributed while others need to be consolidated. It is a flexible and versatile option for logistics management.
Advantages of the hybrid include:
Pallet racking is essential in logistics and storage. Pallets play a fundamental role in transportation, improving the efficiency of goods
This container has all the advantages: large capacity and great maneuverability.